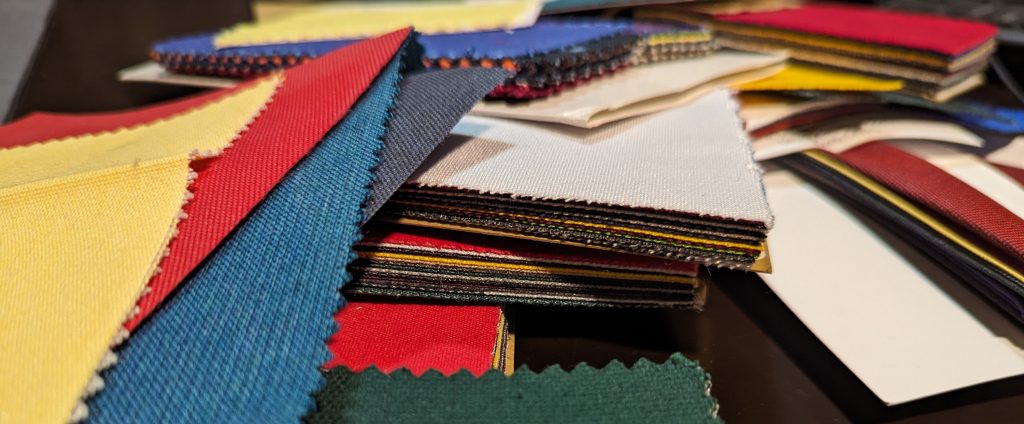
Back when Amanda and I decided to get serious about making Barwa covers, the goal was obvious: Make them exactly like the original covers. Little did we know at the time how much blood, sweat, and tears (quite literally on all three!) would go into the process. We quickly realized that there were going to be supply limitations, and the goal changed to make them as close as possible and remain true to the originals. We’re recording our experience in case anyone is interested in what we found with fabrics and how it led to our current offerings.
Fabric Selection
In the early days, we spent months looking at different materials and mills. We noticed that lighter-weight cotton canvas/duck is available in almost any shade of color imaginable and readily available. This couldn’t be easier, right? WRONG! Unfortunately, these lighter-weight fabrics tend to be quite stretchy and are a terrible fit for the Barwa. We then started trying to match the weight of our original cover and after looking at a *lot* of fabric samples, determined it was a heavier 15 oz. Looking at available options in this range was disappointing. The color options tend to target simple primary colors. Since we’re not designing for the circus or an elementary school from the 80’s, we didn’t see these as viable.
Worse than the color selection was learning about the deficiencies of direct dyes when used for furniture. It was depressing to learn how these dyes can easily transfer colors to your clothing and the colors can just rub off the fibers. We spoke with one of the largest mills in Canada and the response was:
‘Unfortunately, things have changed with cotton duck fabric over the past many decades. The “ideal” product you need simply does not exist. These fabrics used to be dyed with reactive dyes (sometimes VAT dyes) to make them a great option for outdoor use as well (and without the ‘color bleeding’). That is no longer done either. ‘
This was the point where we had to shift gears and find a better alternative.
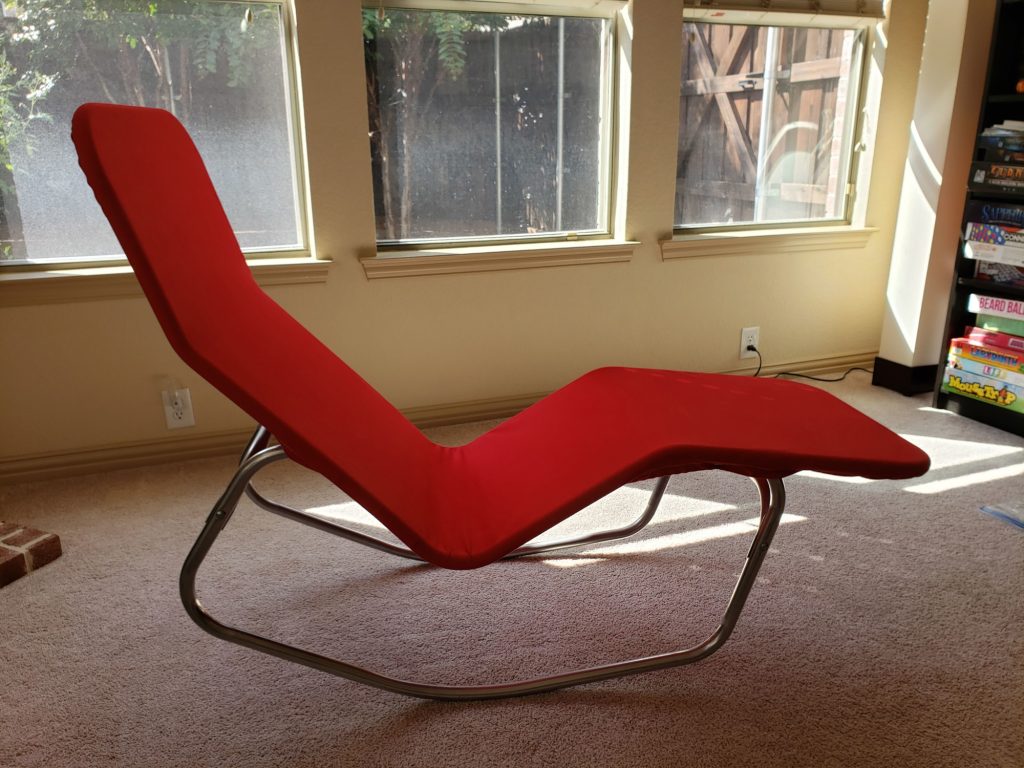
At this point, we expanded the search for fabrics beyond cotton. We looked at anything that we could get our hands on. As I’m writing this years later I don’t remember all the details of our selection criteria, but we were effectively looking for the following:
- Reliable mill and/or supplier – we need consistent quality
- Feel & comfort – the chair has to be comfortable to use, and we want to get as close as possible to the original Barwa “stiffness” that the canvas provides.
- Durability – we want these to last as long as humanly possible
- Weatherproof – Barwas were originally marketed as outdoor furniture and we really want these to hold up to the elements as much as possible.
- Colors – aesthetics matter and ideally we can offer some of the original Barwa colors along with some new options.
We pretty quickly started honing in on acrylic fabrics, particularly awning fabric. On paper, this checked every box. In practice though, it was terrible. First, the fabrics we tried were almost too stiff and didn’t form well to the chair and looked really bad. What’s worse was the texture was rough and almost like sandpaper. I couldn’t stand the feel of it against my arms or legs. From here we started looking at the Sunbrella fabric that’s ubiquitous in outdoor furniture. Sunbrella also checked most of the boxes, and solved the comfort issues, but it felt a little too thin to us (we were testing with a light yellow color while we were working on the covers for the Liljestrand House); Sunbrella was close but still not quite what we wanted.
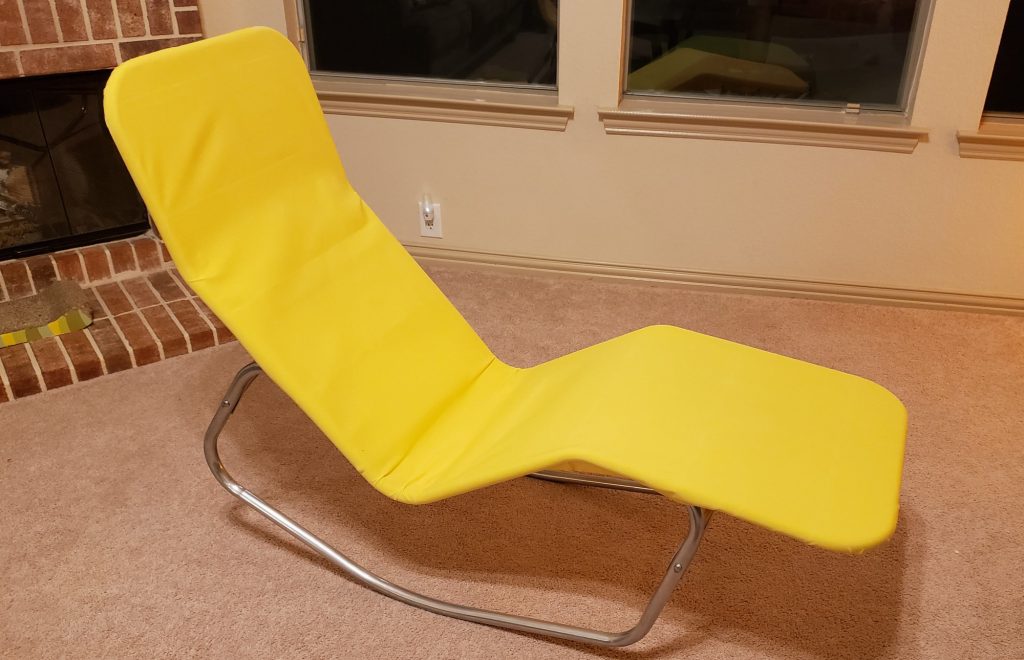
We then found a fabric that comes from a different mill that uses the same fibers as Sunbrella, but has a thicker weave. While the weight of the fabric is identical, this one feels more substantial and has a higher durability rating. More on this fabric later.
The Pattern
Our first attempt at making a cover turned out amazing. The next six or seven; however, were not! It became clear that different fabrics would need the pattern tailored. Also, the target we were trying to hit became more complex as we bought more frames. At first, we naively thought that all of these were the same, and having three frames with some differences made tailoring the pattern challenging. We spent months refining patterns based on different fabrics.
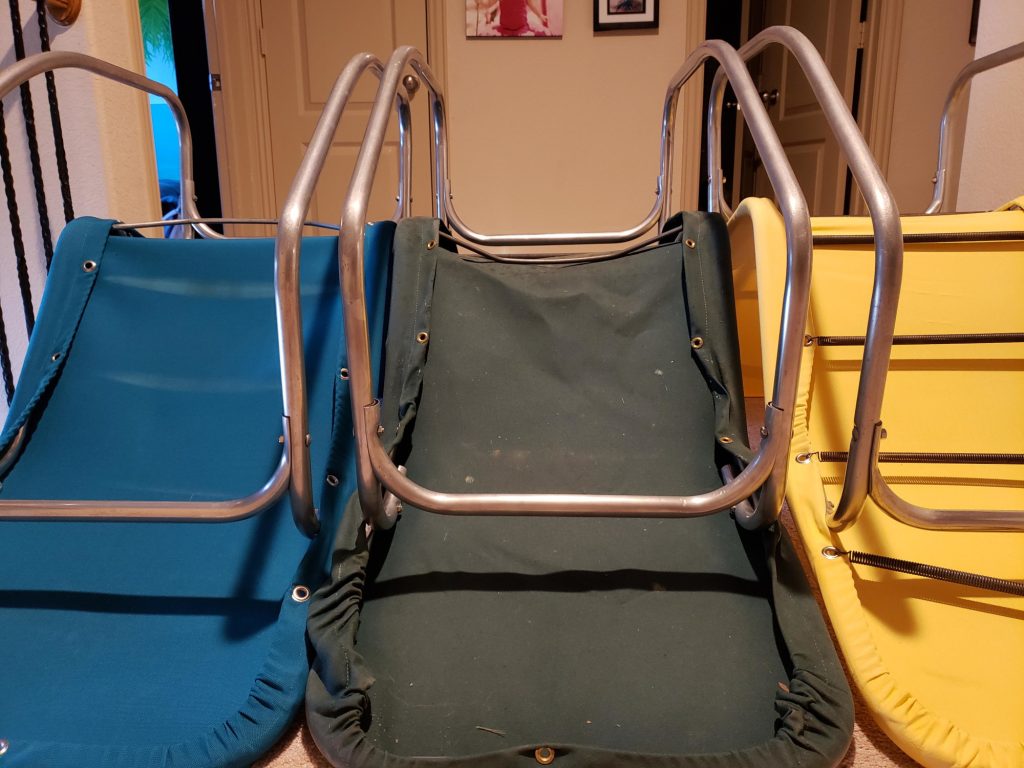
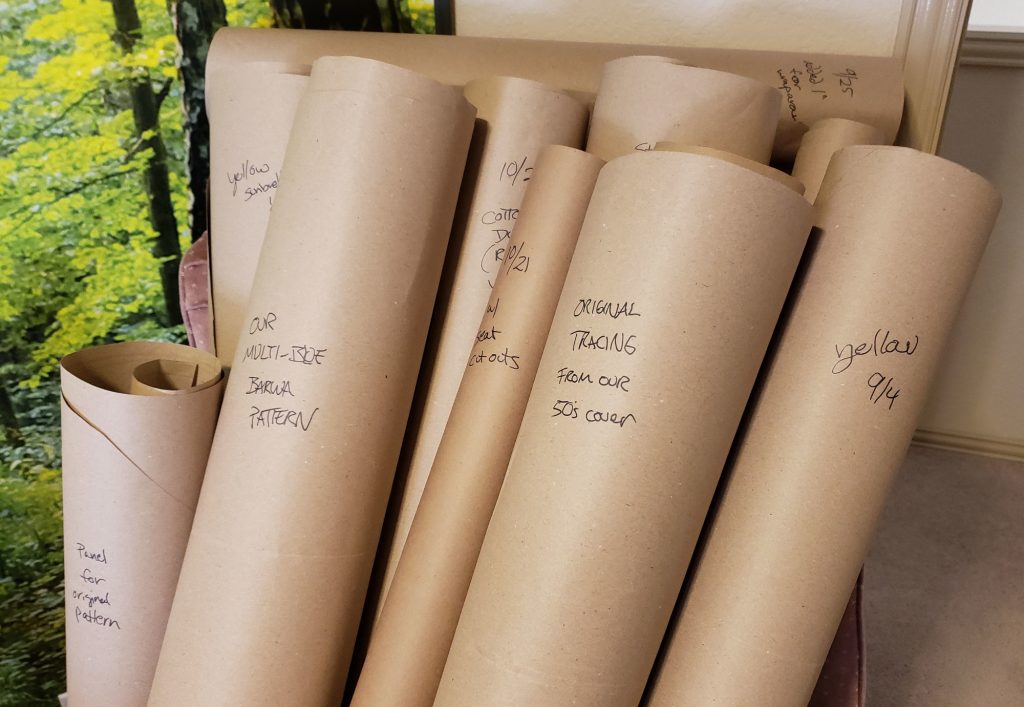
The Franken Cover
Buying fabrics in small amounts is actually pretty expensive and the shipping only makes it worse because the fabric we work with isn’t supposed to be folded. At one point we were out of Sunbrella, but still had some wastage. We decided to stitch two pieces together for the next prototype. We knew it would be hideous, but I very clearly remember this pattern test being “the one”. While we were happy with a lot of the aspects of Sunbrella it felt thin and was visually very transparent, especially when backlit. Our next step was to see if we could recreate the success of this cover & pattern using the heavier acrylic mentioned earlier. I remember telling Amanda, “We did it!” when we saw it on our chair.

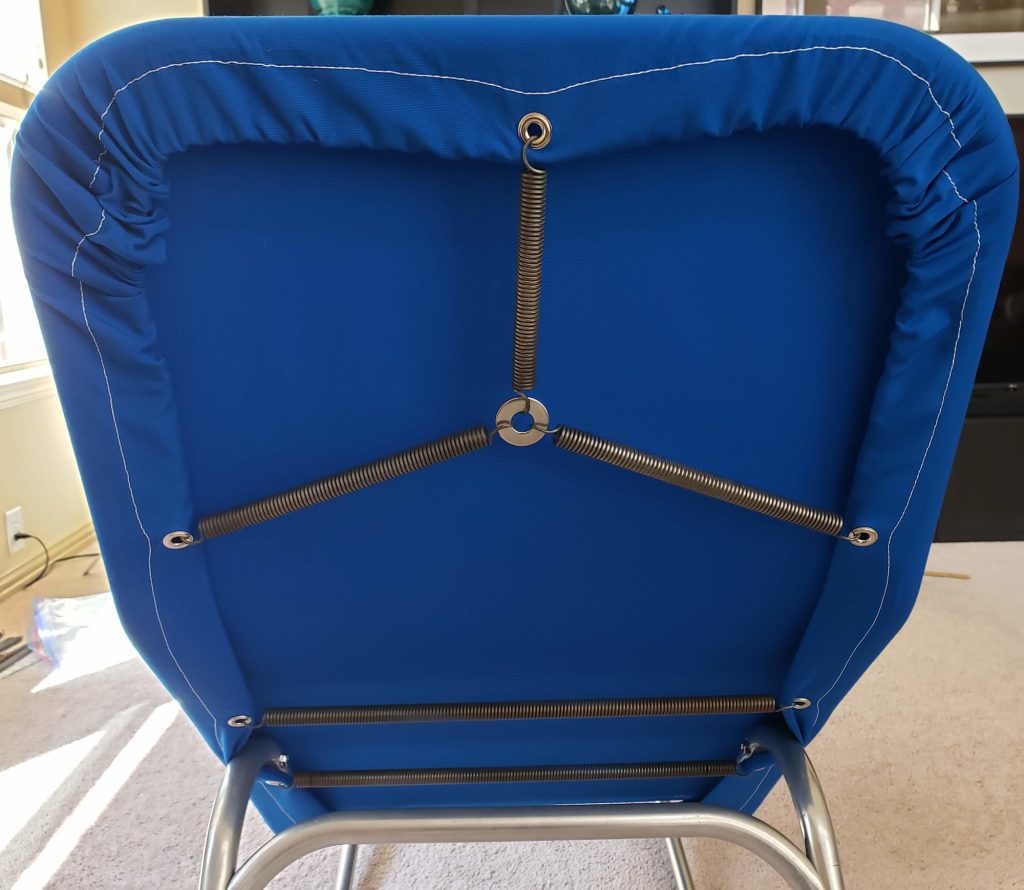
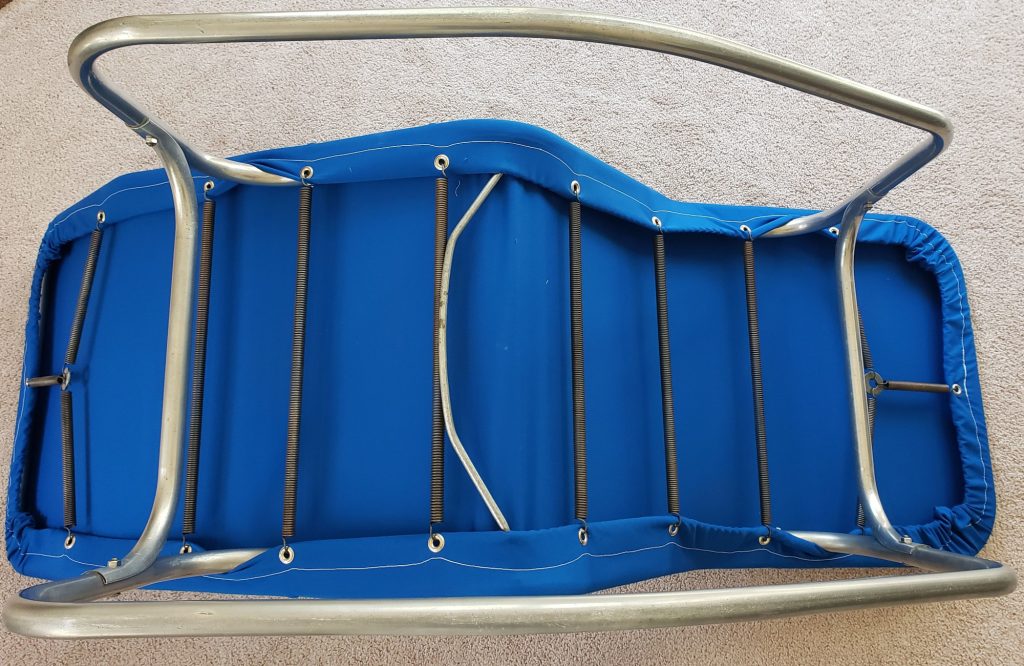
Best of Both Worlds
As much as we love the acrylic fabric we use, there’s still something about the original cotton covers that is amazing. We found a mill that produces a cotton duck with an almost identical weave and weight to our original cover. We made a number of prototypes using 15 & 17 oz weights, and we preferred the 15 for a number of reasons. If we go with undyed cotton, we could get the benefits the original covers have, but not have to deal with the shortcomings of modern dyes.
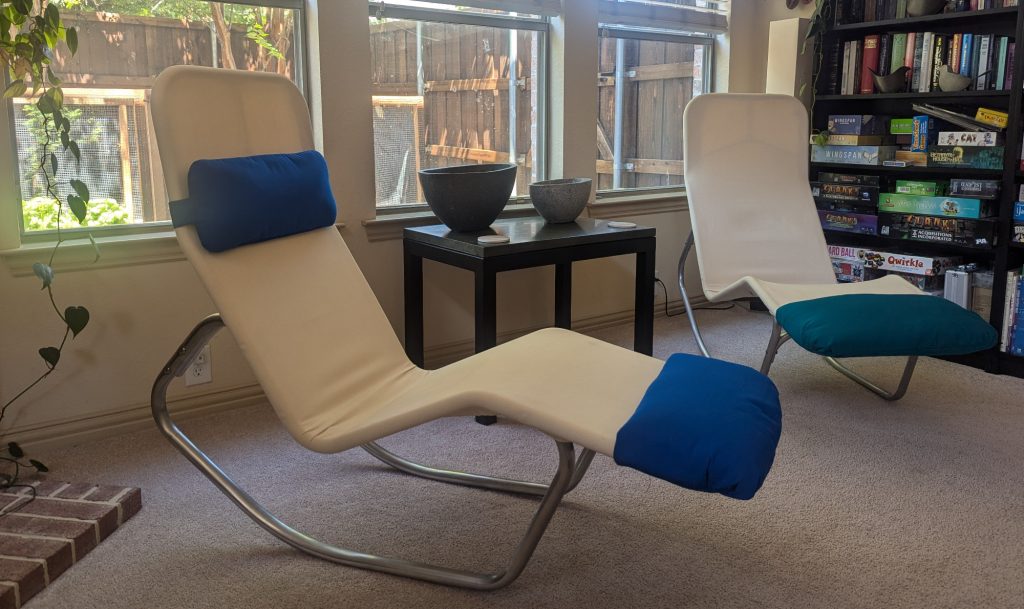
Validation from History
About two years into making covers, we were sent a catalog from the 90’s. Honestly, we had no idea these chairs were being made in that decade. This catalog showed us that cotton canvas was offered in 15 & 18 oz weights, and they also introduced a Sunbrella option to better withstand the outdoor elements. This was really validating for us to learn. On one hand, it would have been nice to have found some new, superior fabric options, but on the other our ~6 months of testing everything we could get our hands on led us down a path that was both true to the original covers and arguably improved considering modern availability of fabrics.
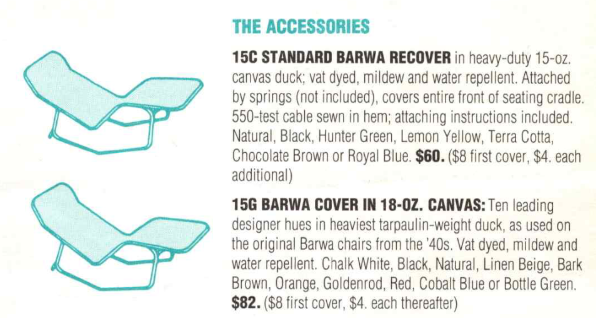
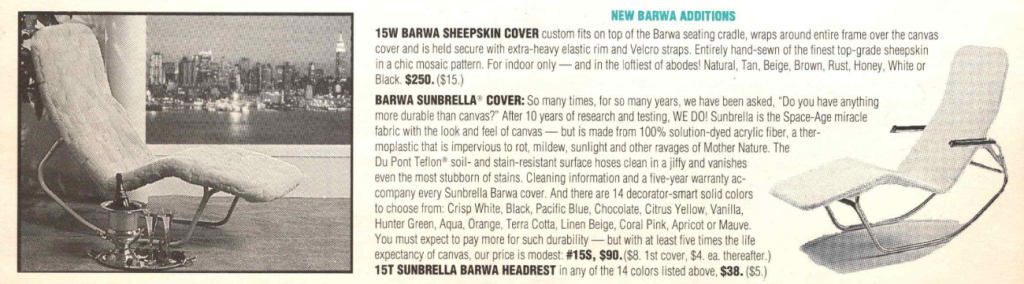
Looking Forward
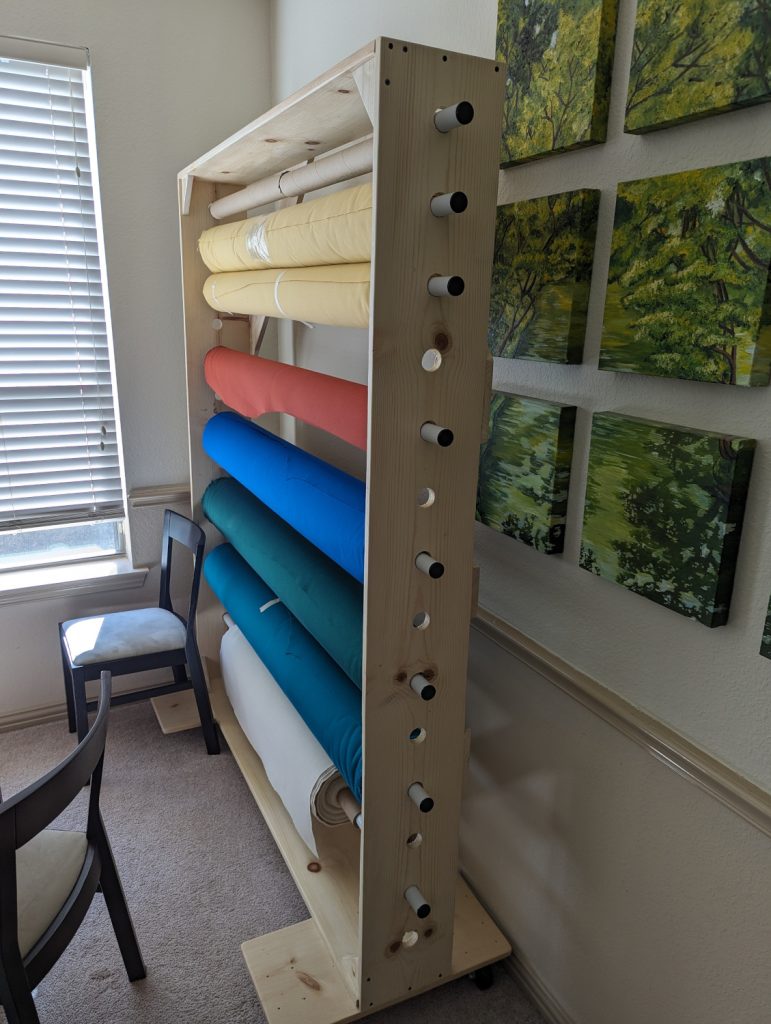
We’re very happy with the fabrics we use and have gotten a lot of positive feedback from customers. Part of me still wishes a 12 or 15 oz acrylic was offered in a furniture grade. Such a fabric would likely be absurdly expensive, but I would love to try it and maybe offer some smaller runs. The other thing we’ve wanted to try but haven’t gotten around to it is a soft denim. Maybe one day we will have the time to attempt this. ….one day!