Shortly after we started making replacement covers we began getting requests for the complete chair. At the time I thought, “It’s just a few bends in aluminum tubing. How hard could it be?!” Looking back three years later all I can do is smile at my naivety and think to myself that ignorance is truly bliss. I won’t detail every step of the way, but this post will give you some idea of our journey to recreate Barwa frames.
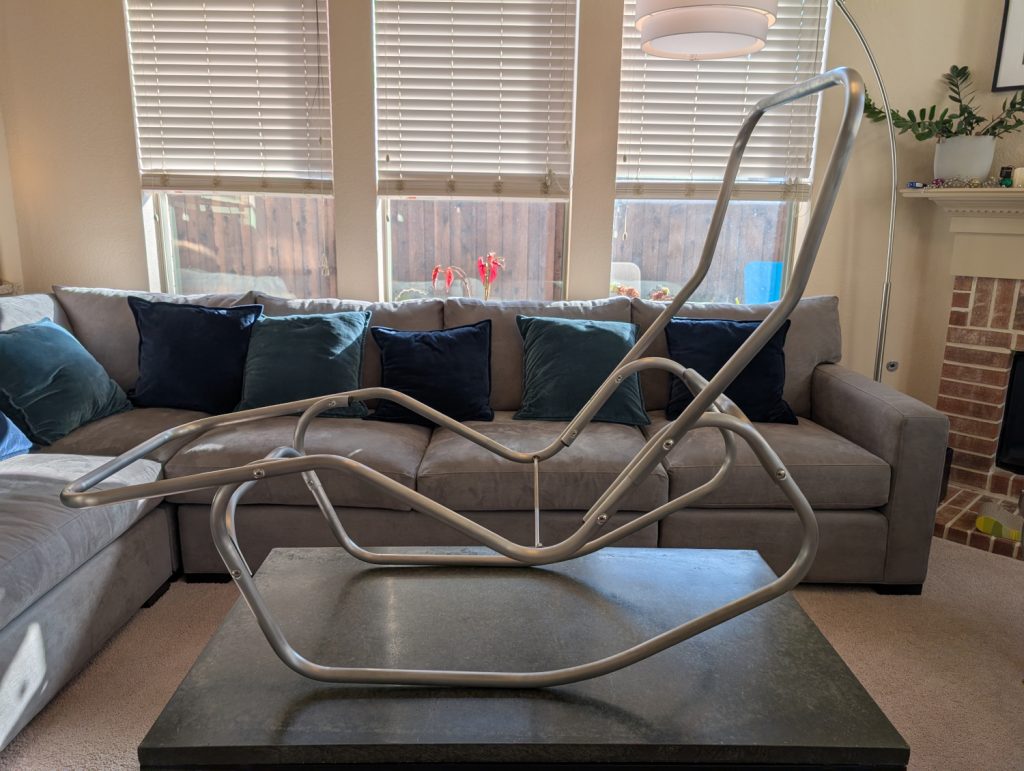
We started from zero. No experience, no knowledge, and not a lot of direction. Luckily we live in a time where knowledge is more accessible than ever before thanks to the internet. After some initial research we were fortunate to find a friend of a friend who owns a successful hotrod shop. He is a master at building custom exhaust systems, welding, roll cages, and retro fitting different engines and drive trains into cars. I heard a buddy ask him, “What’s it like to work on a hundred thousand dollar cars?” To which he replied, “I don’t know. I only work on three hundred thousand dollar cars!” There’s clearly some hyperbole there, but probably not much based on what I’ve seen in his shop. We were grateful for the help of two really talented and knowledgeable people who helped us reverse engineer the frame, choose some of the tools, and also fabricate some custom tools & jigs for us. After a few “lessons” on the bender we began to setup shop in our garage and started acquiring a slew of equipment including a bender, roller, drill press, arbor press, compressor, and various tables, vices, and an ever growing “maybe someday” list of wants to make our garage comfortable to work in – namely things like insulation and air conditioning.
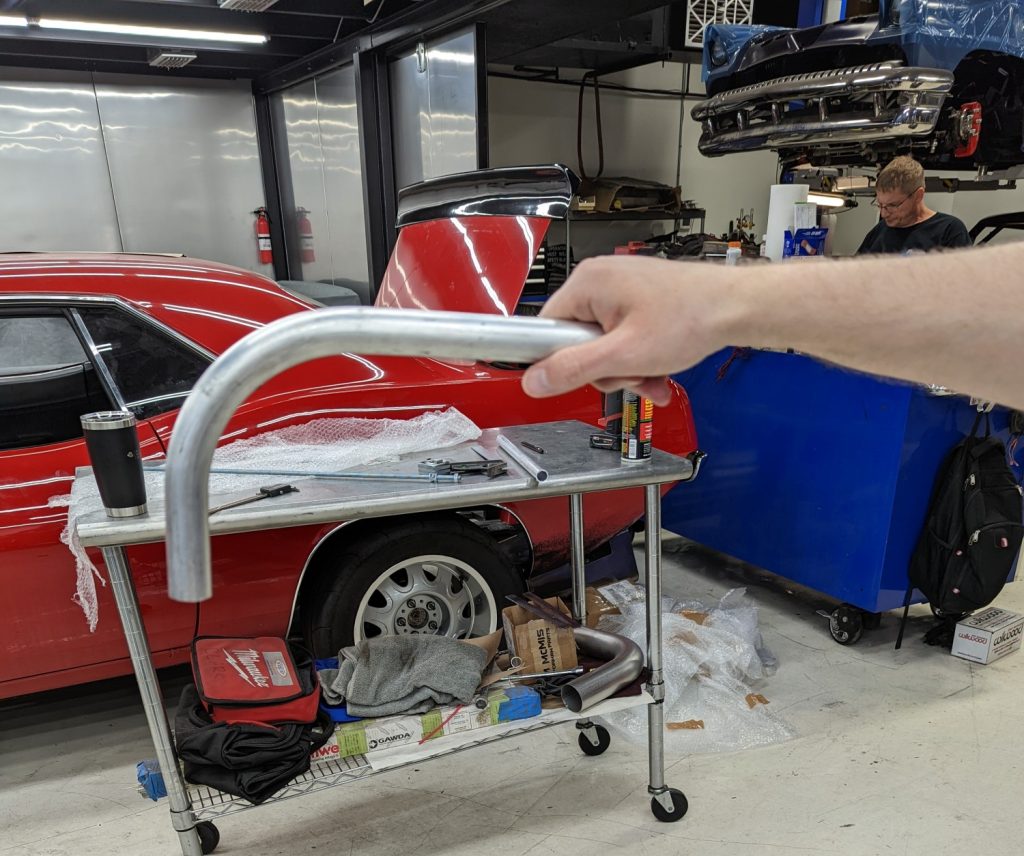
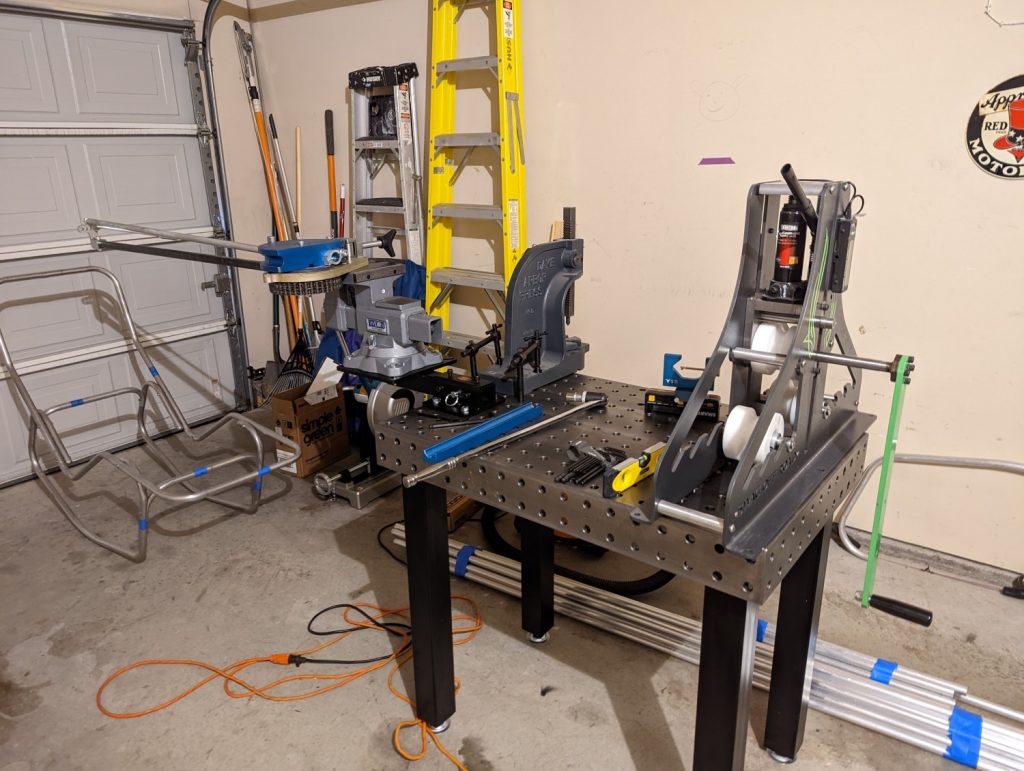
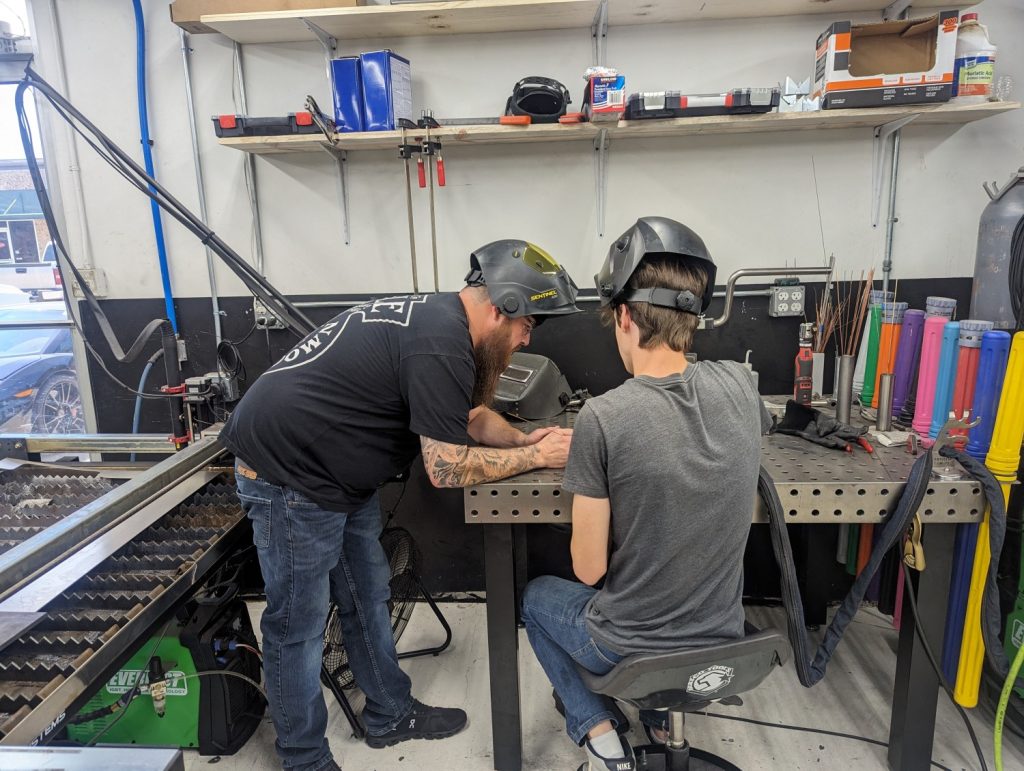
In September of 2022, we had our little shop up and running with the specs to start making frames. Not bad!
Frame #1 – completed Nov ’22
At this point, we’re probably six months into the process and ready for the first attempt. To the untrained eye, this one would be difficult to tell from an original. It looked great and functioned just fine. Unfortunately the recline was a bit too “fast” compared to an original one and the holes had to be widened quite a bit to allow bolts to pass through properly. While I’m really proud of the results, it definitely wasn’t good enough and our processes were very rough and difficult to repeat. I didn’t closely track the time on this frame, but I’d estimate about 80 hours of work went into it.
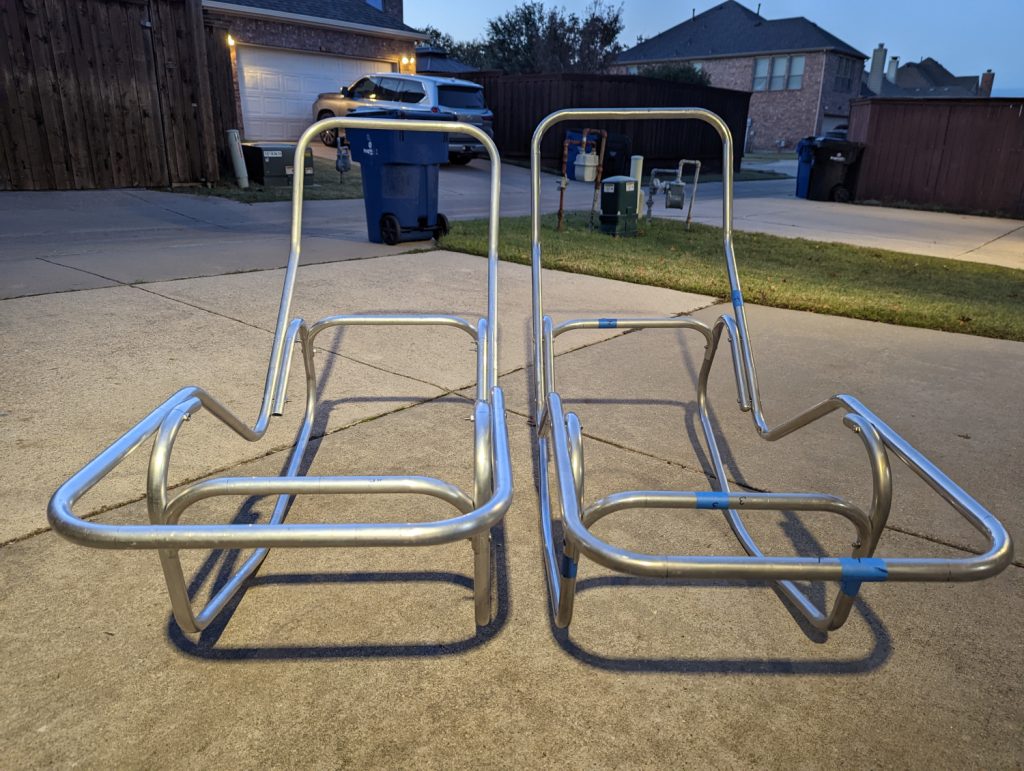
It was at this point that I happened to meet an engineer who specializes in manufacturing efficiencies. What are the odds! He was kind enough to help us perfect our bending to get what I believe is as repeatable of a process as possible, using a bender like ours. It took quite a while to change the bender and recalculate all the parts, but we were really impressed with the results and very glad we did this. The next blocker was figuring out how to get cleaner, more aligned holes so the bolts could cleanly pass through four walls.
Frame #2 – completed June ’24
Life happens and we both got really busy with other things and could only chip away at this very slowly as time allowed. I got a big boost of confidence making a new set of replacement legs for a customer in the summer of 2023, and the details on that project are here. Once these were finished in August, I continued chipping away on the many points of the process that needed to be refined.
My sister wanted a Barwa and I thought this would be a good opportunity to get some feedback on our next prototype. I really wanted this one to be better all around and solve the problems with holes from the first one. I worked on a few CAD designs for some jigs to facilitate drilling holes clean through each area. These were a step in the right direction, but ultimately were not as good as I was hoping. We were also further delayed waiting on a new 3D printer. Ultimately, the new jigs worked, but I wasn’t happy with the amount of “flex” they had and how the bushings would heat up and come loose from the PETG material we used.
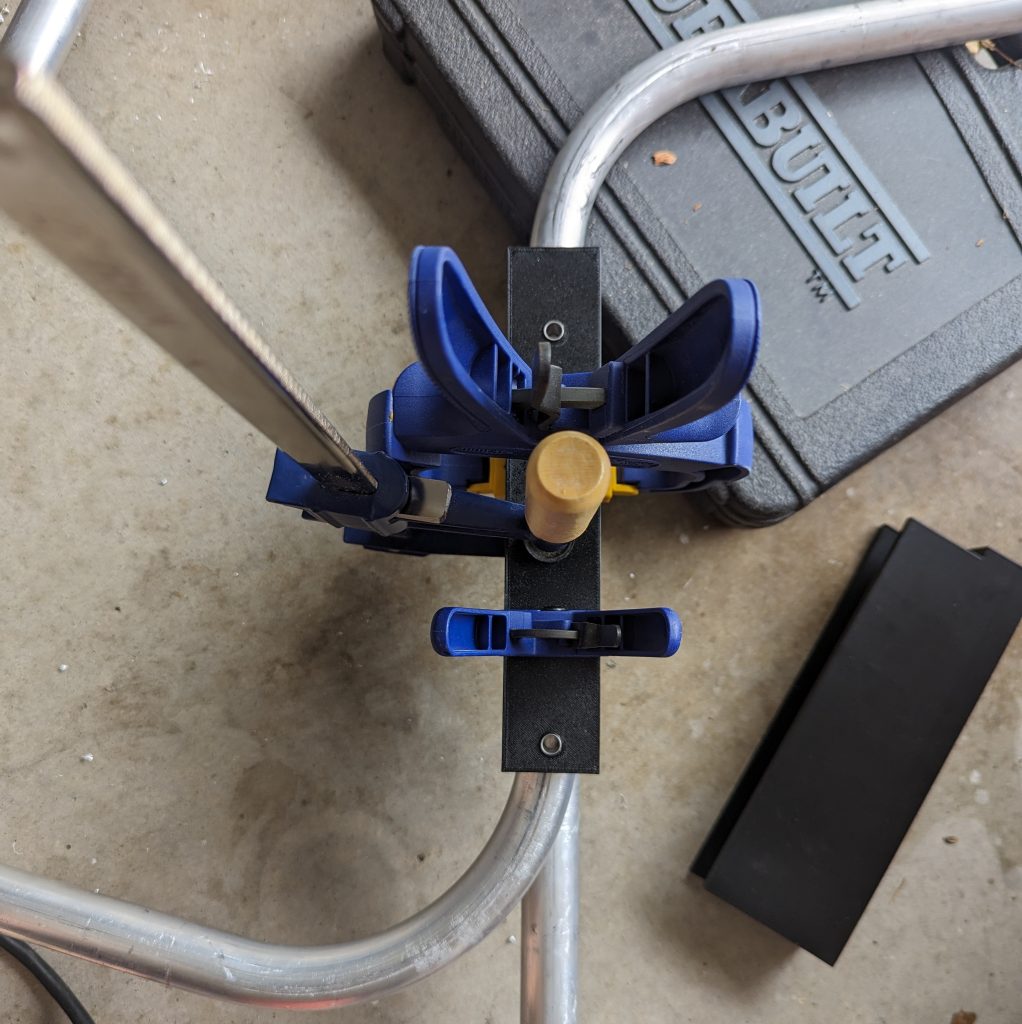
We were really happy with how the bends came out, the chair bolted up beautifully, and most importantly, it felt exactly like a real Barwa when using it. We couldn’t tell a difference. This one took about ~60 hours to complete and I also walked away with five pages worth of notes for improvements I need to make in the future.
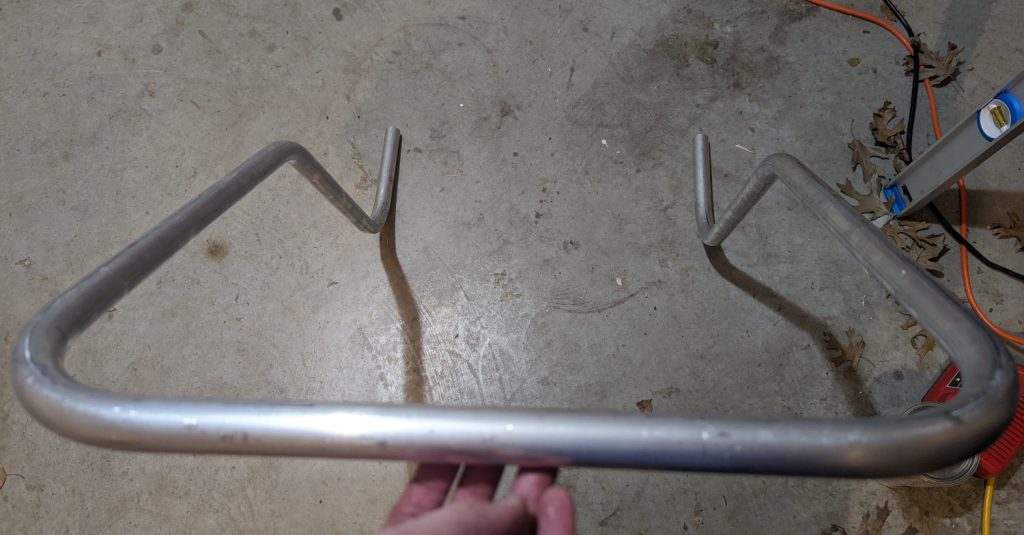
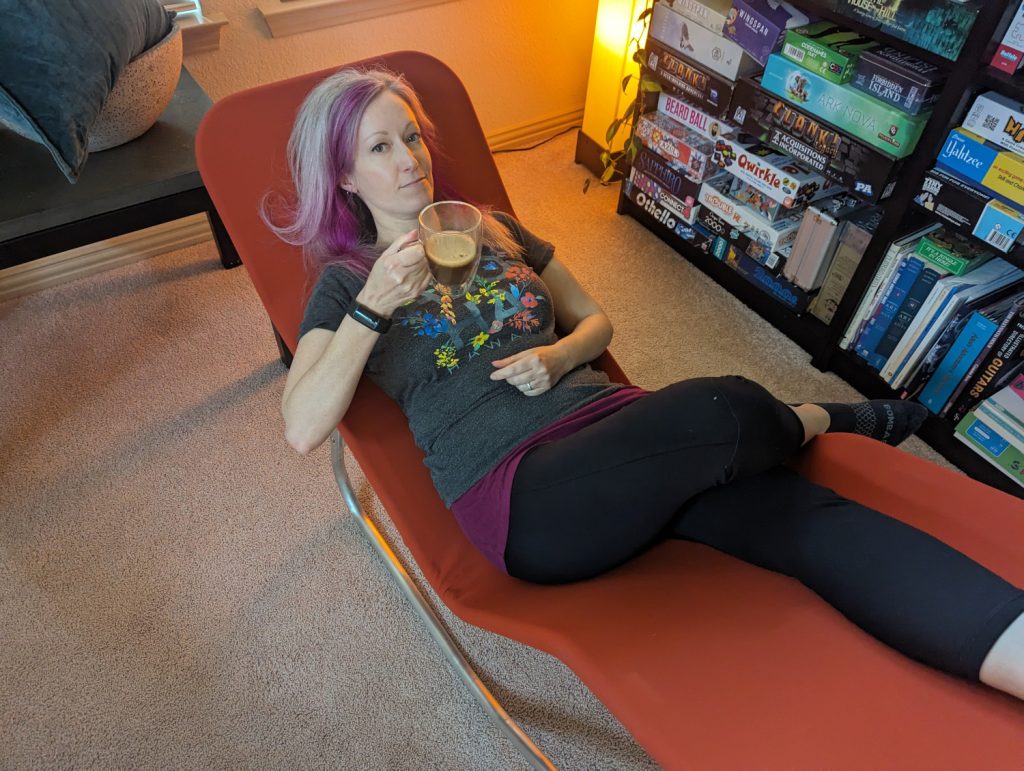
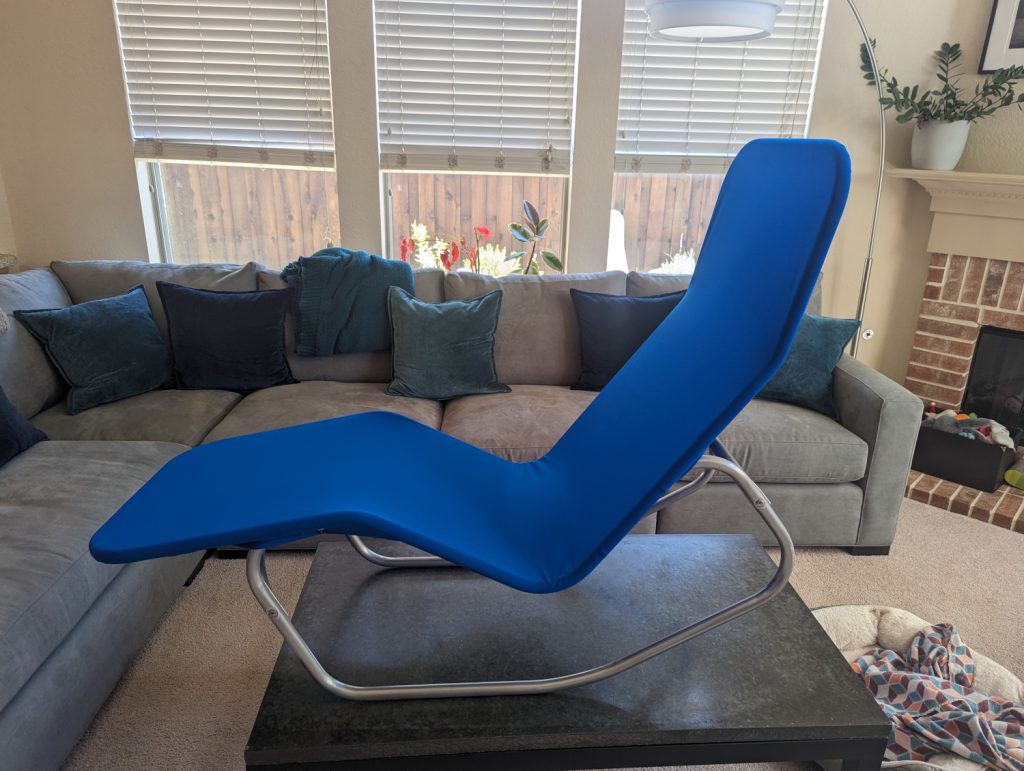
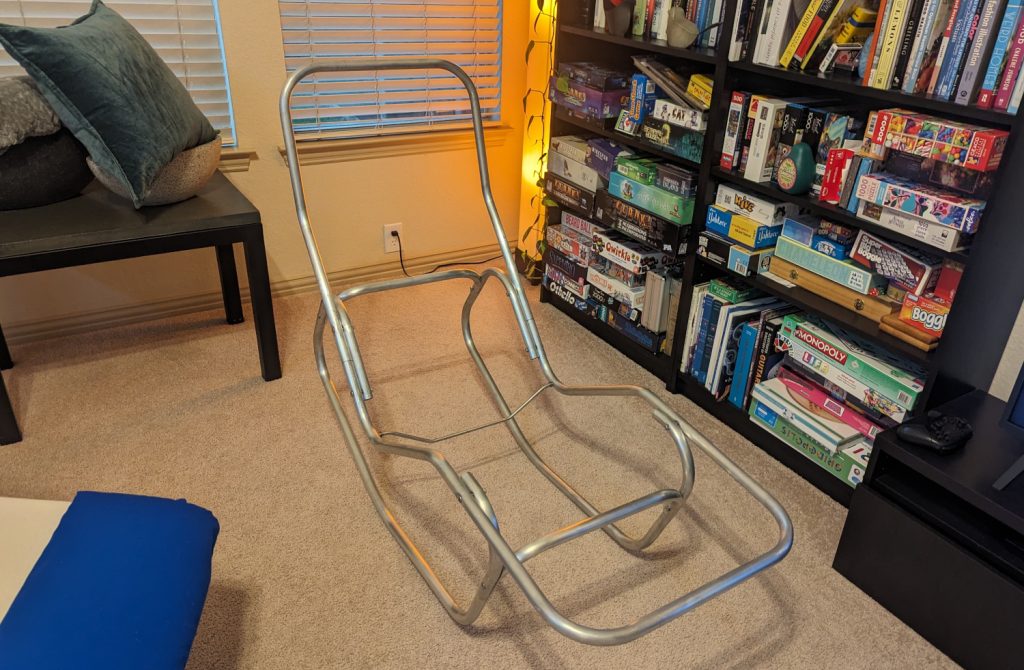
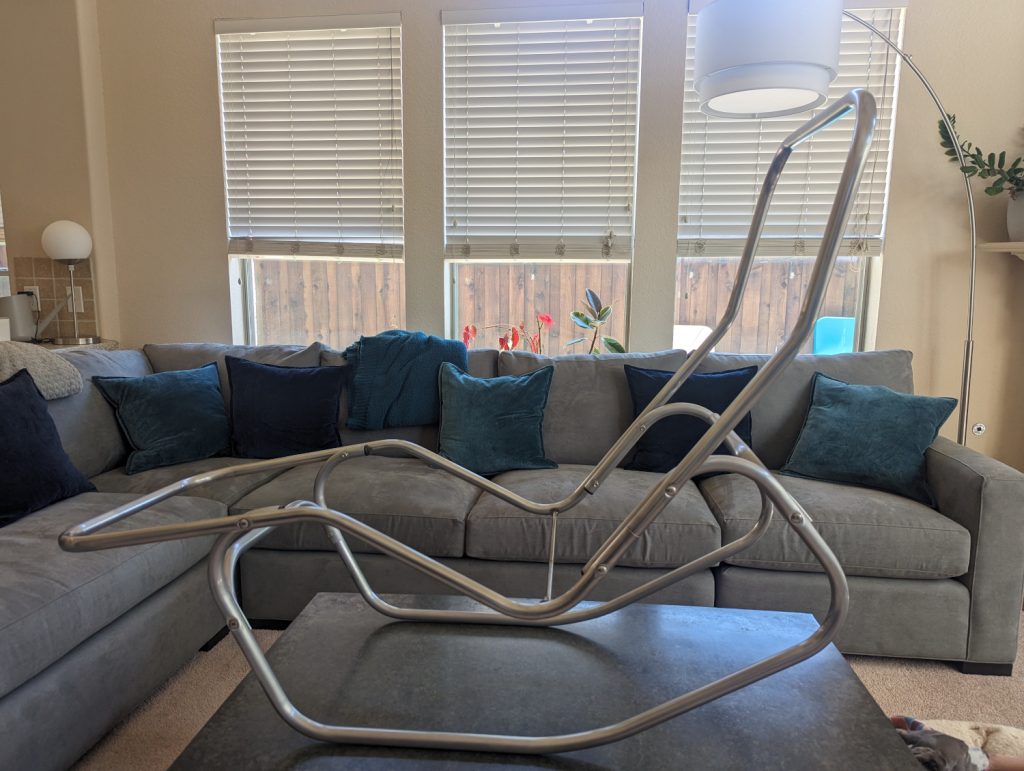

The difference between frames 1 & 2 was really encouraging for us, but we knew there was a lot of room for improvement in our processes.
Frame #3 – complete Sep ’24
To really get the holes where we needed, it was clear we were going to need a proper two-sided punch. Only two companies, one in Italy and another in Canada, seem to make what we need. We decided to go ahead and “invest” (that’s my nice way of saying “spent a ton of money”) in a machine to do this the right way. We tested it on the third frame and it easily shaved off about 10 hours of labor. Amazing! The next thing to optimize is polishing. Going through 7 to 12 levels of grits is incredibly time intensive and arguably not worth the effort. We got some advice for a new technique that should give us basically the same result in much less time. It worked very well. I didn’t time the total hours on this frame exactly, but I’d estimate ~25 hours of labor.
My parents had voiced some interest in getting one, and since they gave us the chair that kicked everything off for us, we were honored to get them a new one. The new punch and polishing methods worked really well. It’s still a lot of work, but it’s also exciting to see the time saving results.
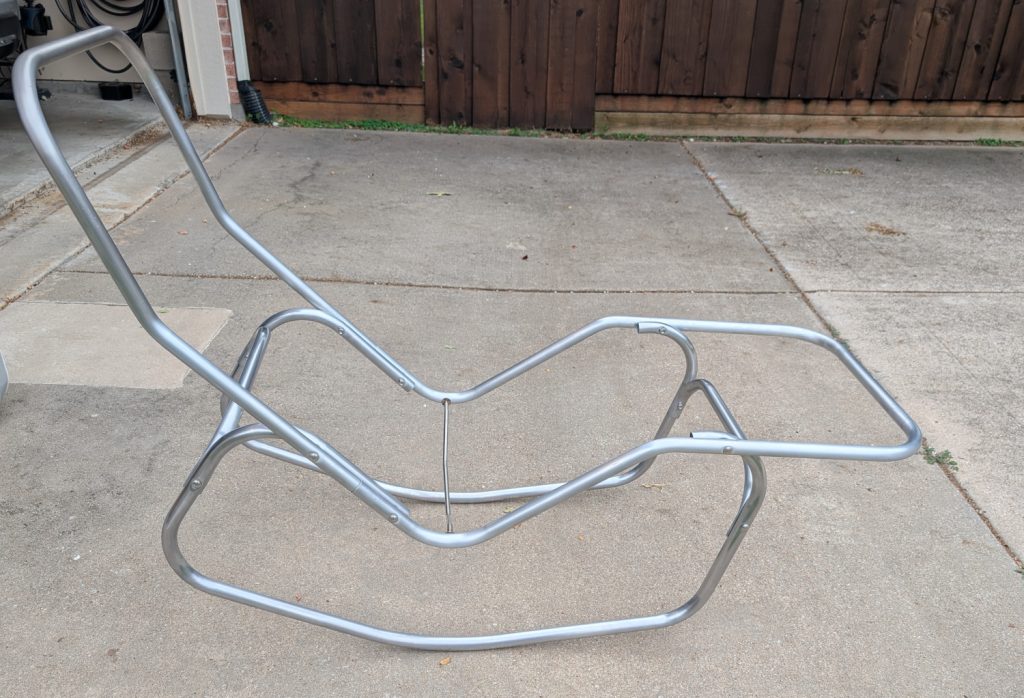
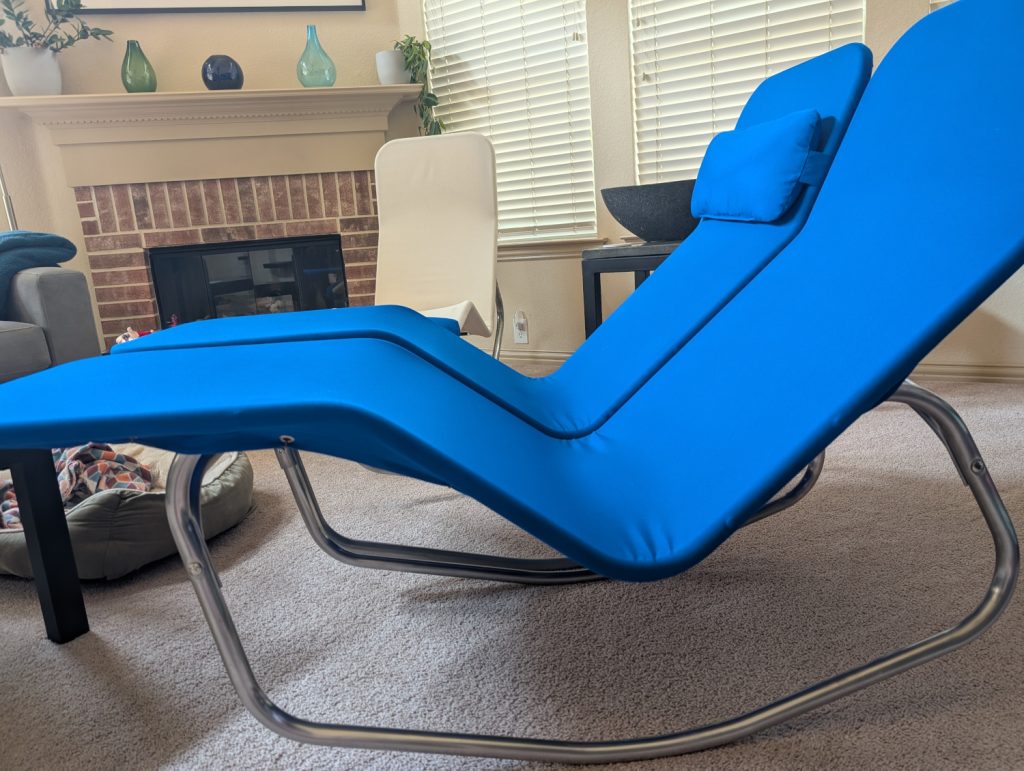
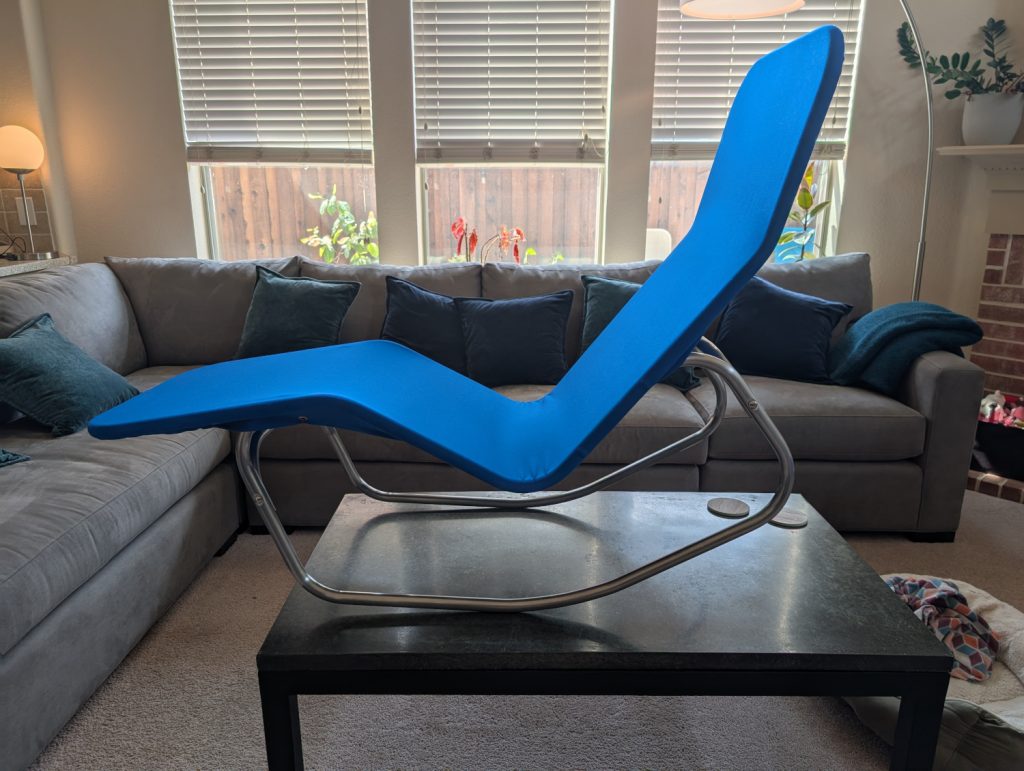
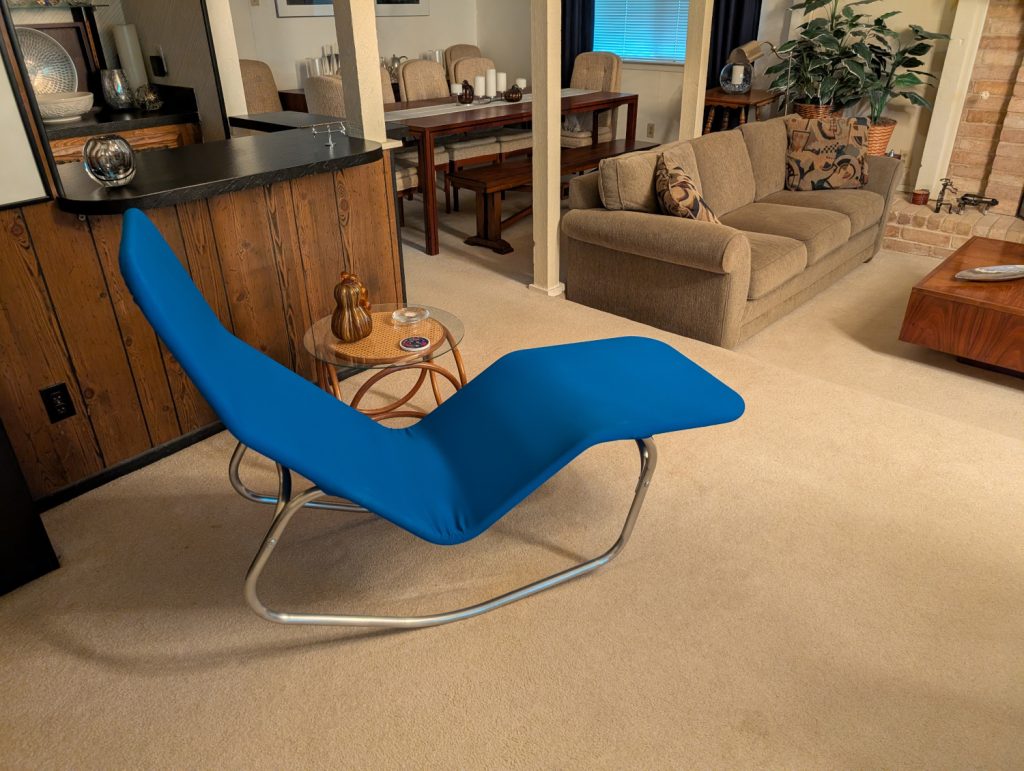
Frame #4 – completed Dec ’24
As I write this we have just completed our fourth frame and couldn’t have been happier with it. I didn’t track the time as closely as I should have, but I would estimate between 15-20 hrs. This frame was destined for one of our early customers who had been looking for a second chair for a few years. The big challenge to solve with this one was shipping, as this was our first one that we weren’t able to deliver assembled and via car.
With this frame we could really feel all of the improvements in our process come together. It’s still too labor intensive to hit “scale”, but we’re really proud of the results. It was also a big relief when it arrived safely and the owner was happy with it.
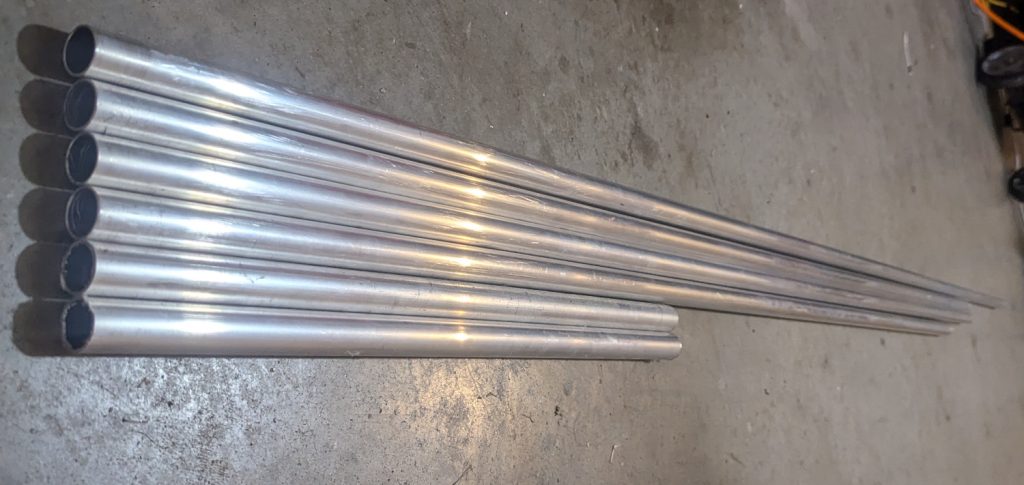
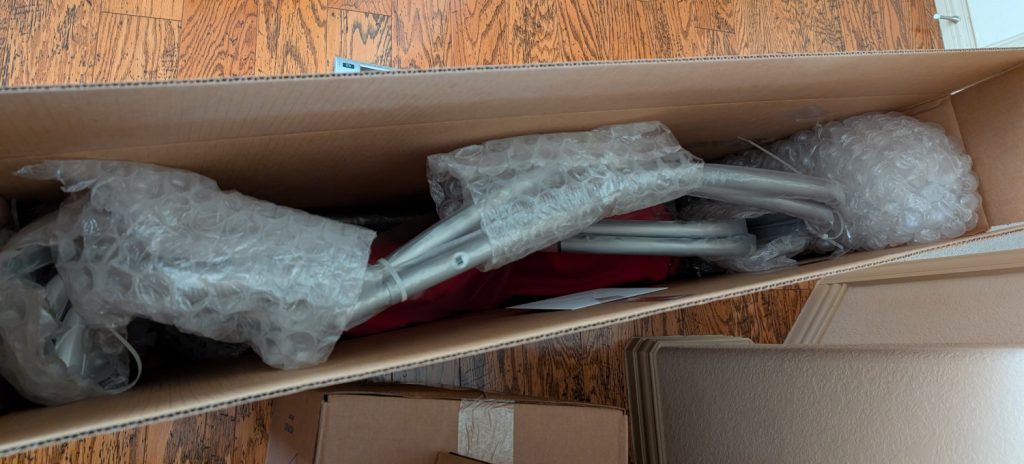
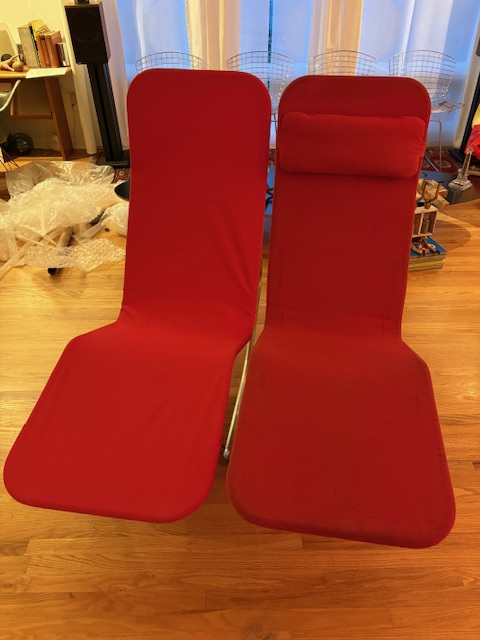
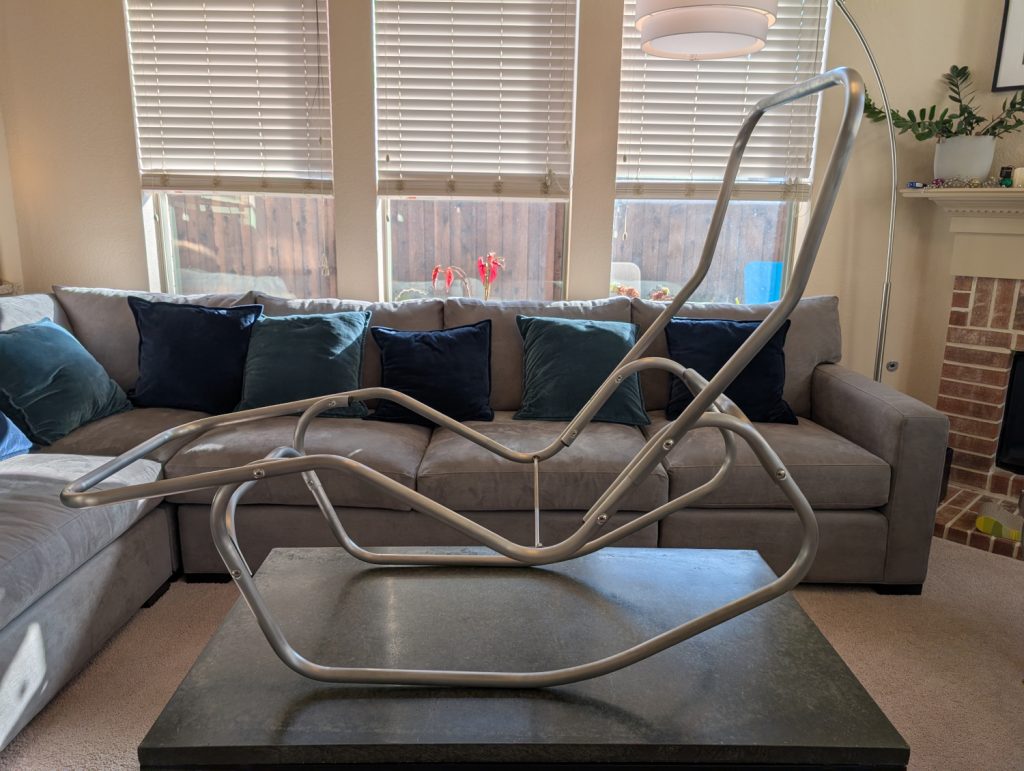
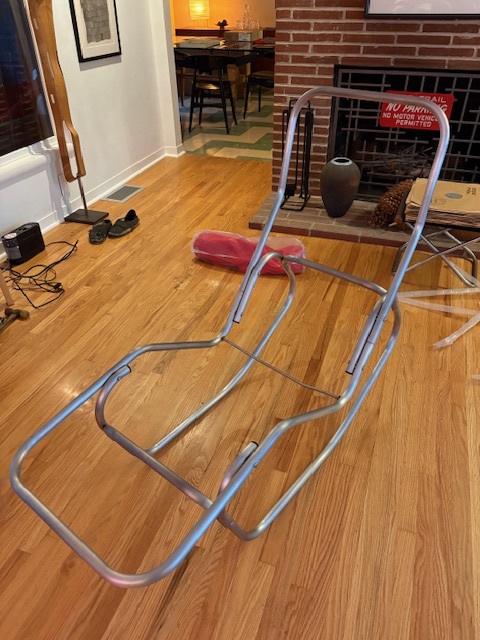
What’s Next?
One of the biggest advancements that didn’t exist when the original chairs were made are CNC machines. These machines have automated vast amounts of manufacturing across all industries. The tube bending CNCs can be programmed with incredibly high precision to bend each piece of the frame. We are looking into the possibility of using CNCs to do the initial bends for us, and then continuing to do everything else by hand. The main advantage here would be a higher consistency and degree of accuracy in all the pieces. This part is still a work in progress for us, but we have the goal of producing a small batch of 25 chairs in 2025. Please reach out if you would like to be on the waiting list, and thanks for reading about our journey to reintroduce our favorite mid-century modern lounger.
We’d like to say a special thanks to Trae, Kenne, Steve, Nathan, Chuck, Tim, Will, Richard, Gerard, and Todd and all the thoughts and input along the way. We couldn’t have gotten this far without your help!!
Thank you for taking the time writing your story! It was a trip back in time to re-appreciate my grandparent’s barwas. As kids, we spent the night on them outside on their upper deck in the hot summer months of Oklahoma. Thank you for your labor of love to recreate them. Hopefully we will win the lottery some day!😀.
Thanks for reading this and for reaching out. …..I too have my hopes up for the lottery. 😉
Sign me up.
I love the interest and effort.
I have a girlfriend who covers mine.
Therefore, put me on your list, let me know what deposit you need.
John Horne
That’s a girlfriend worth keeping!! 😉 In all seriousness, thanks for reaching out. I’ve added you to our waiting list using the gmail account you used in this comment. Shoot us a note at barwachair@gmail.com if you’d like us to use a different email. I’m hoping we can get the first batch out before summer.
I would like to be on your waitlist for a frame. Although I continue to browse vintage listings, and if I find one in my range, I’ll be ordering cover and positional pillow from you! Thanks for your dedication to resurrecting this art chair.
If you are a Barwa chair, lover… then we are friends… no further introductionsneeded! As a kid, my family had a bright orange Barwa. and I guess the feeling is universal 0f that moment you recline for the first time and think you’re gonna flip over.. I remember flying in a jumbo jet into Boston and looking out the window… I could see that my house was easily identifiable because of the bright orange Barwa on the deck! I still have that chairs frame but I am in need of a bright orange cover. I bought a second Barwa chair at a garage sale with a faded periwinkle blue cover. Unfortunately, it was destroyed one night by a runaway snowplow. I applaud your industrious nature and enthusiasm for good design.
The very best, Garth